Kanban
Ottimizzazione ed efficienza nel riassortimento.
Kanban
Ottimizzazione ed efficienza nel riassortimento.
Il sistema Kanban
Il sistema Kanban, una componente essenziale del sistema Just In Time (JIT), è impiegato con l’obiettivo di ottimizzare le fasi di approvvigionamento e reintegrazione delle scorte. Questa metodologia mira a migliorare l’efficienza dei processi di produzione assicurando la disponibilità delle materie prime al momento opportuno. Il suo obiettivo primario è allineare la capacità produttiva con la domanda effettiva, riducendo sia la sovrapproduzione che i tempi morti tra le fasi di lavorazione.
Si applica principalmente in contesti caratterizzati dalla logica del Pull, in cui la produzione inizia solo in seguito al ricevimento dell’ordine definitivo dal cliente.
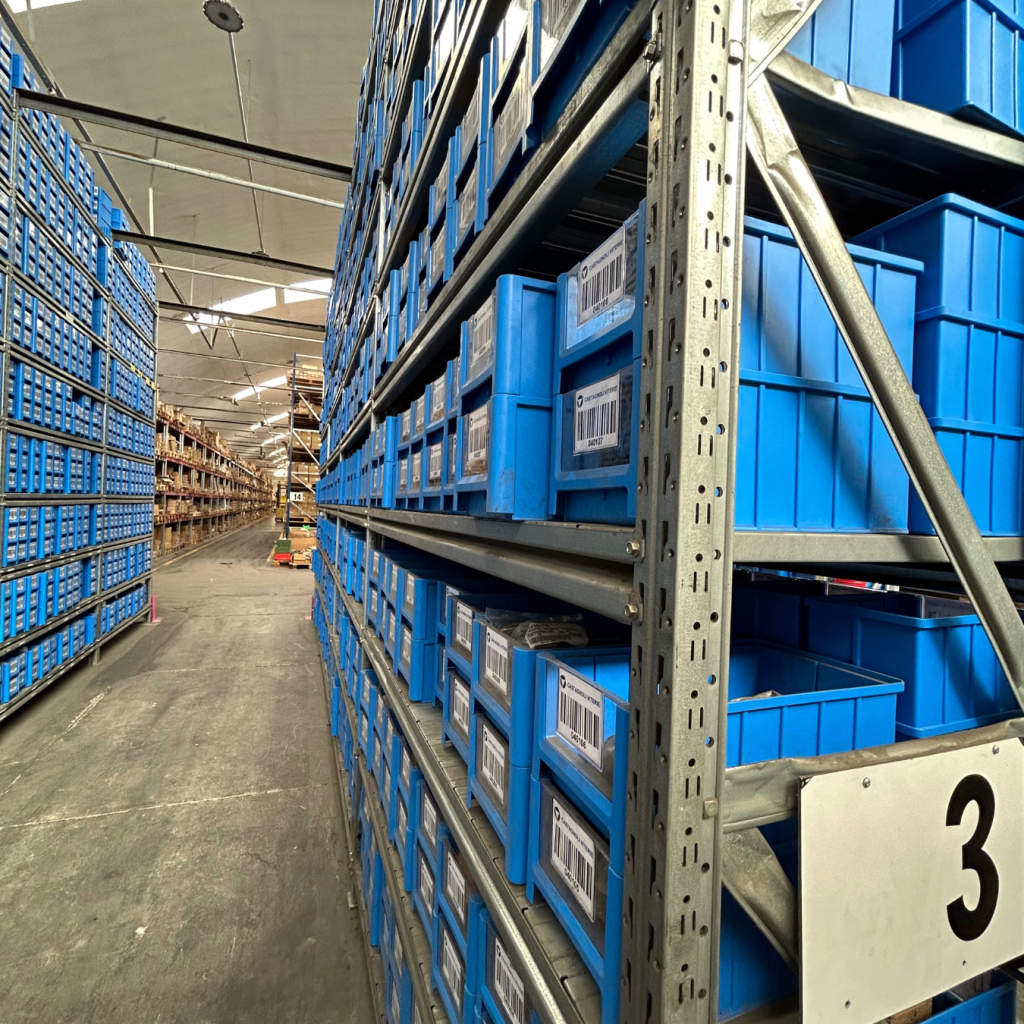
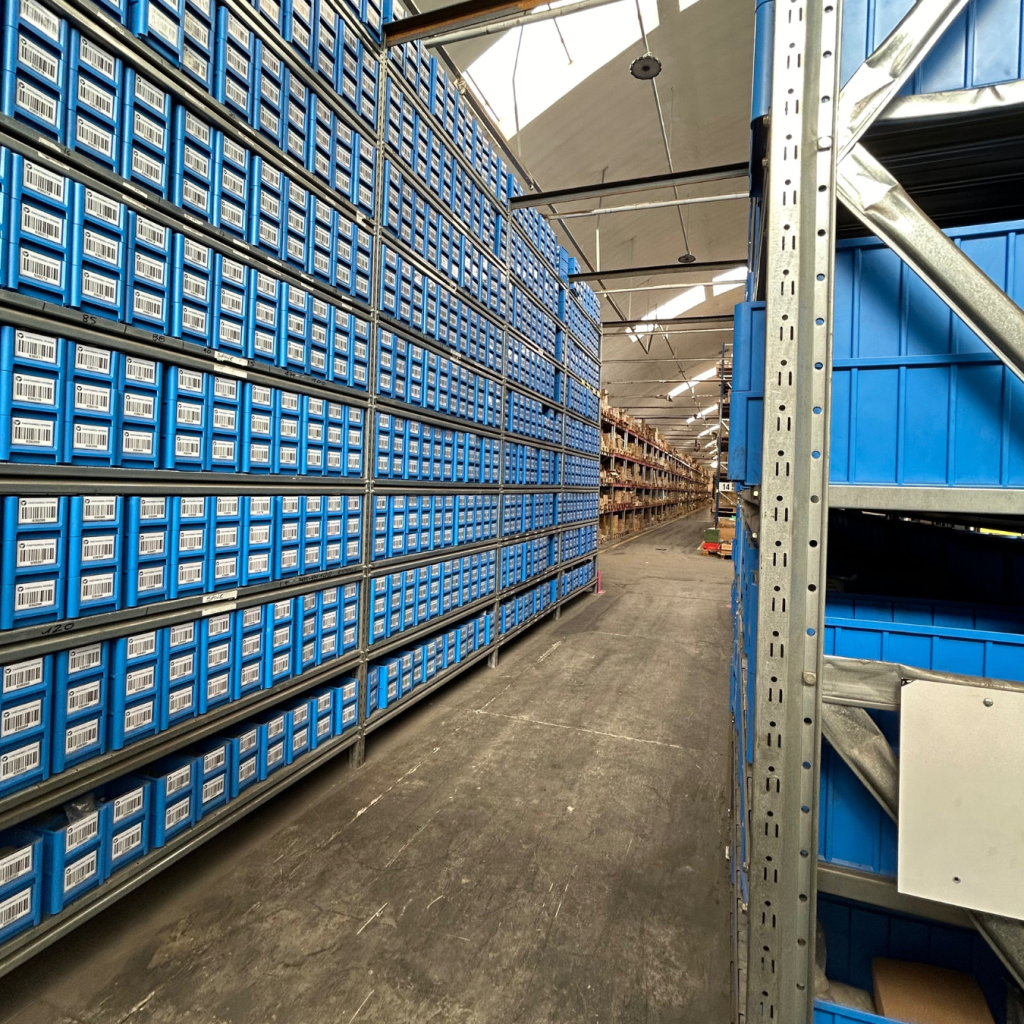
Definizione e origine del sistema Kanban
L’ingegnere giapponese Taiichi Ohno sviluppò il sistema Kanban prendendo spunto dalle pratiche di approvvigionamento adottate nei supermercati americani. In tali contesti, i clienti selezionano i prodotti dai ripiani etichettati, e una volta passati alla cassa, vengono registrate le informazioni sullo stato delle scorte del punto vendita, consentendo così di generare ordini per il magazzino. Questo è possibile grazie alla condivisione di un sistema di etichettatura tra magazzino e punto vendita.
Successivamente, il magazzino invia ordini di rifornimento ai fornitori o produttori, in un ciclo che coinvolge l’intera catena di approvvigionamento, con l’obiettivo finale di garantire la disponibilità dei prodotti nei punti vendita. Per mantenere il controllo sulle scorte e evitare situazioni di “scaffale vuoto”, è fondamentale stabilire dei punti di riordino ben definiti.
Il sistema Kanban per la viteria
Il principio fondamentale di questo sistema di rifornimento delle linee di produzione è conciso ma altamente efficiente: utilizzando un sistema a rotazione con due contenitori, la viteria è resa disponibile just in time direttamente presso la postazione di stoccaggio. Una volta esaurito il materiale contenuto nel primo contenitore, il secondo è già pronto e disponibile sullo scaffale, poiché Castagnoli, prima che il primo contenitore si esaurisca, si è già provveduto a ricaricare lo scaffale. Questo approccio consente di:
- Rispondere prontamente alle variazioni della domanda
- Garantire un approvvigionamento sicuro
- Ridurre le scorte di magazzino
- Ottimizzare l’impiego di capitale.
Il flusso dei materiali è gestito con estrema semplicità attraverso due contenitori dotati di etichetta Kanban, supportata da codici a barre. Tutti i dati pertinenti, tra cui cliente, postazione di stoccaggio, articolo, denominazione, tipo di contenitore, lotto e quantità di riempimento, vengono specificati con la massima precisione.
Il sistema Kanban
Il sistema Kanban, una componente essenziale del sistema Just In Time (JIT), è impiegato con l’obiettivo di ottimizzare le fasi di approvvigionamento e reintegrazione delle scorte. Questa metodologia mira a migliorare l’efficienza dei processi di produzione assicurando la disponibilità delle materie prime al momento opportuno. Il suo obiettivo primario è allineare la capacità produttiva con la domanda effettiva, riducendo sia la sovrapproduzione che i tempi morti tra le fasi di lavorazione.
Si applica principalmente in contesti caratterizzati dalla logica del Pull, in cui la produzione inizia solo in seguito al ricevimento dell’ordine definitivo dal cliente.
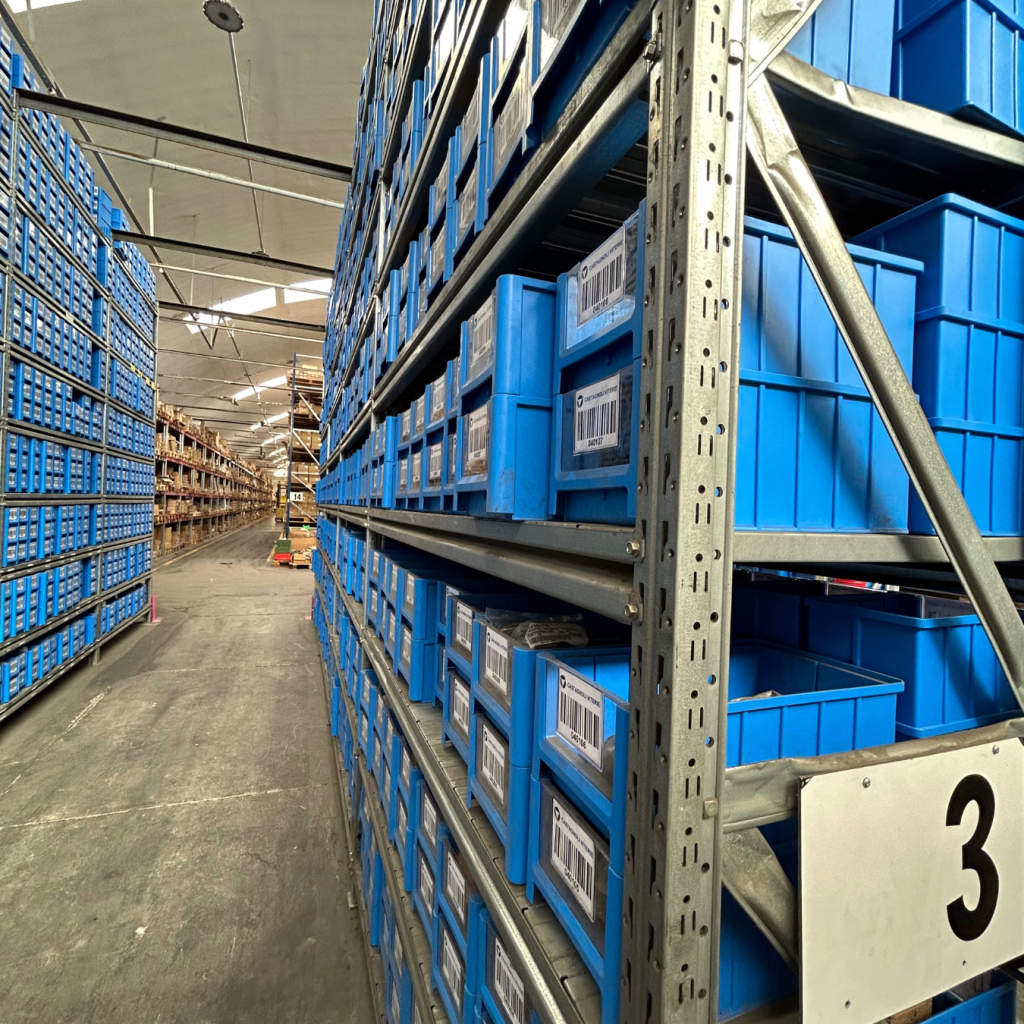
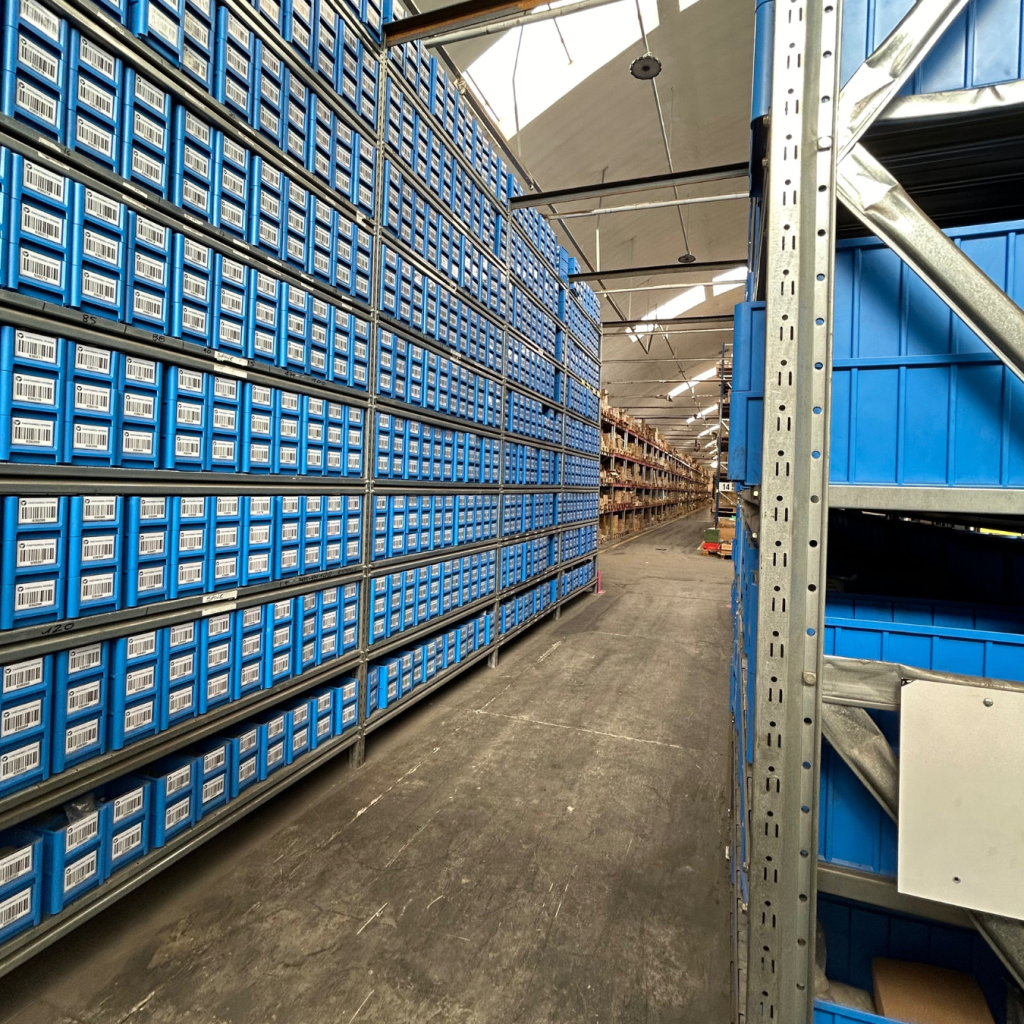
Definizione e origine del sistema Kanban
L’ingegnere giapponese Taiichi Ohno sviluppò il sistema Kanban prendendo spunto dalle pratiche di approvvigionamento adottate nei supermercati americani. In tali contesti, i clienti selezionano i prodotti dai ripiani etichettati, e una volta passati alla cassa, vengono registrate le informazioni sullo stato delle scorte del punto vendita, consentendo così di generare ordini per il magazzino. Questo è possibile grazie alla condivisione di un sistema di etichettatura tra magazzino e punto vendita.
Successivamente, il magazzino invia ordini di rifornimento ai fornitori o produttori, in un ciclo che coinvolge l’intera catena di approvvigionamento, con l’obiettivo finale di garantire la disponibilità dei prodotti nei punti vendita. Per mantenere il controllo sulle scorte e evitare situazioni di “scaffale vuoto”, è fondamentale stabilire dei punti di riordino ben definiti.
Il sistema Kanban per la viteria
Il principio fondamentale di questo sistema di rifornimento delle linee di produzione è conciso ma altamente efficiente: utilizzando un sistema a rotazione con due contenitori, la viteria è resa disponibile just in time direttamente presso la postazione di stoccaggio. Una volta esaurito il materiale contenuto nel primo contenitore, il secondo è già pronto e disponibile sullo scaffale, poiché Castagnoli, prima che il primo contenitore si esaurisca, si è già provveduto a ricaricare lo scaffale. Questo approccio consente di:
- Rispondere prontamente alle variazioni della domanda
- Garantire un approvvigionamento sicuro
- Ridurre le scorte di magazzino
- Ottimizzare l’impiego di capitale.
Il flusso dei materiali è gestito con estrema semplicità attraverso due contenitori dotati di etichetta Kanban, supportata da codici a barre. Tutti i dati pertinenti, tra cui cliente, postazione di stoccaggio, articolo, denominazione, tipo di contenitore, lotto e quantità di riempimento, vengono specificati con la massima precisione.
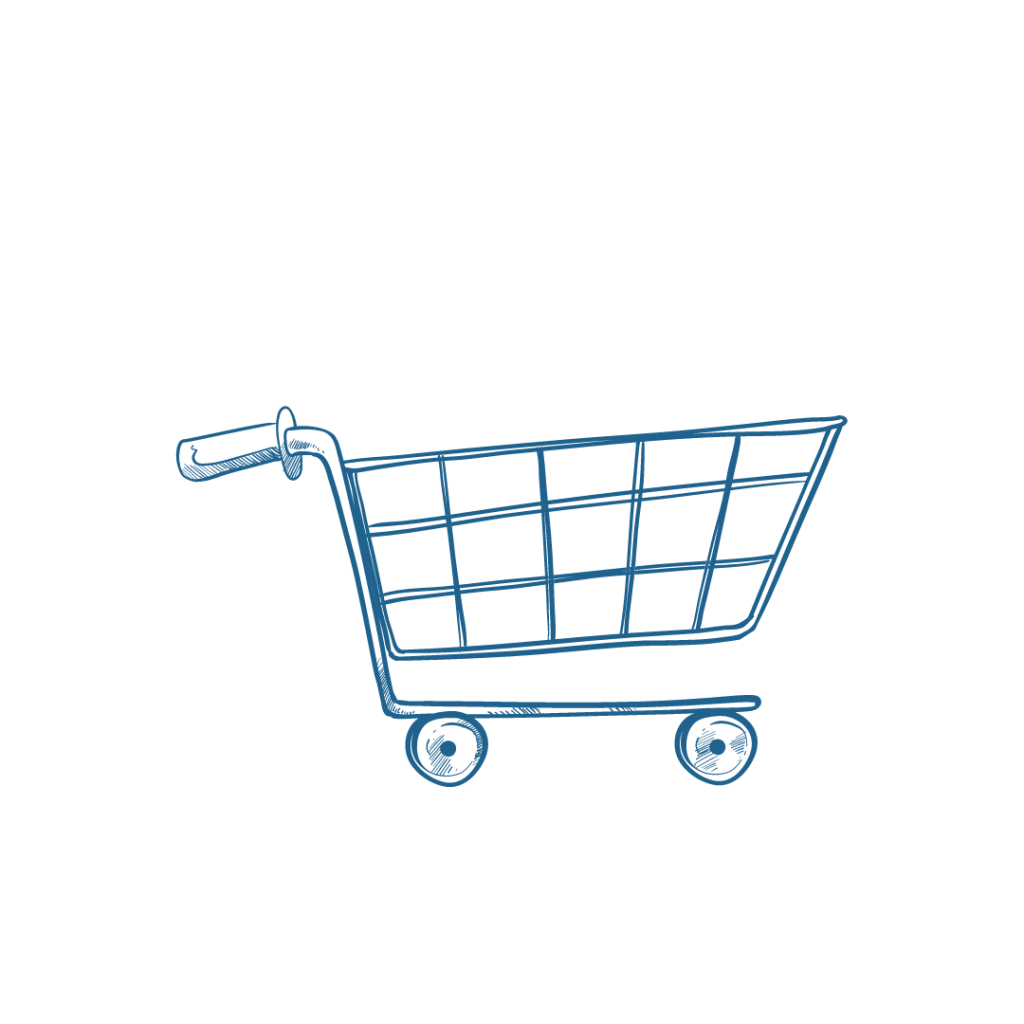