Kanban
Optimization and efficiency in replenishment.
Kanban
Optimization and efficiency in replenishment.
The Kanban system
The Kanban system, an essential component of the Just-In-Time (JIT) methodology, is utilized to optimize procurement and stock replenishment phases. This approach aims to enhance the efficiency of production processes by ensuring the availability of raw materials at the right time. Its primary objective is to align production capacity with actual demand, thereby reducing overproduction and minimizing downtime between processing phases.
It is primarily applied in contexts characterized by a pull-based logic, where production starts only after receiving a final order from the customer.
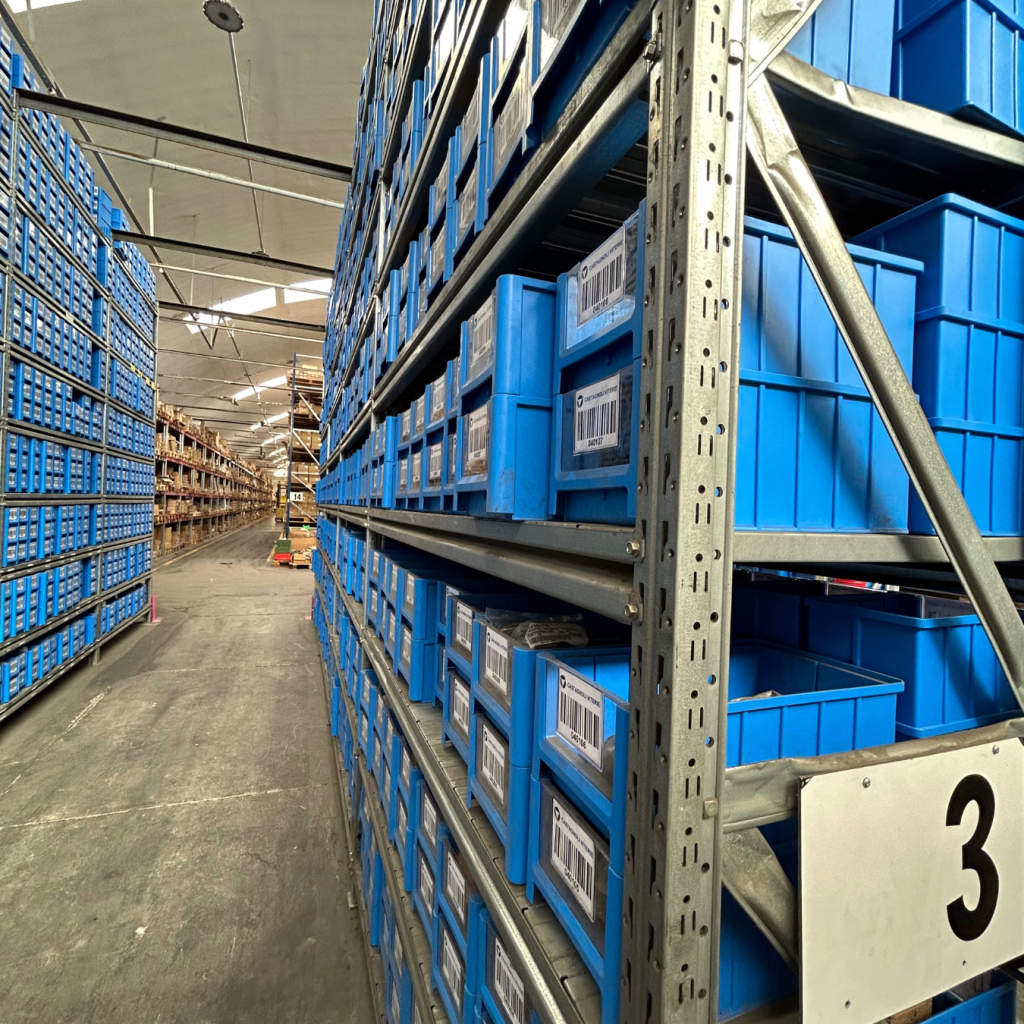
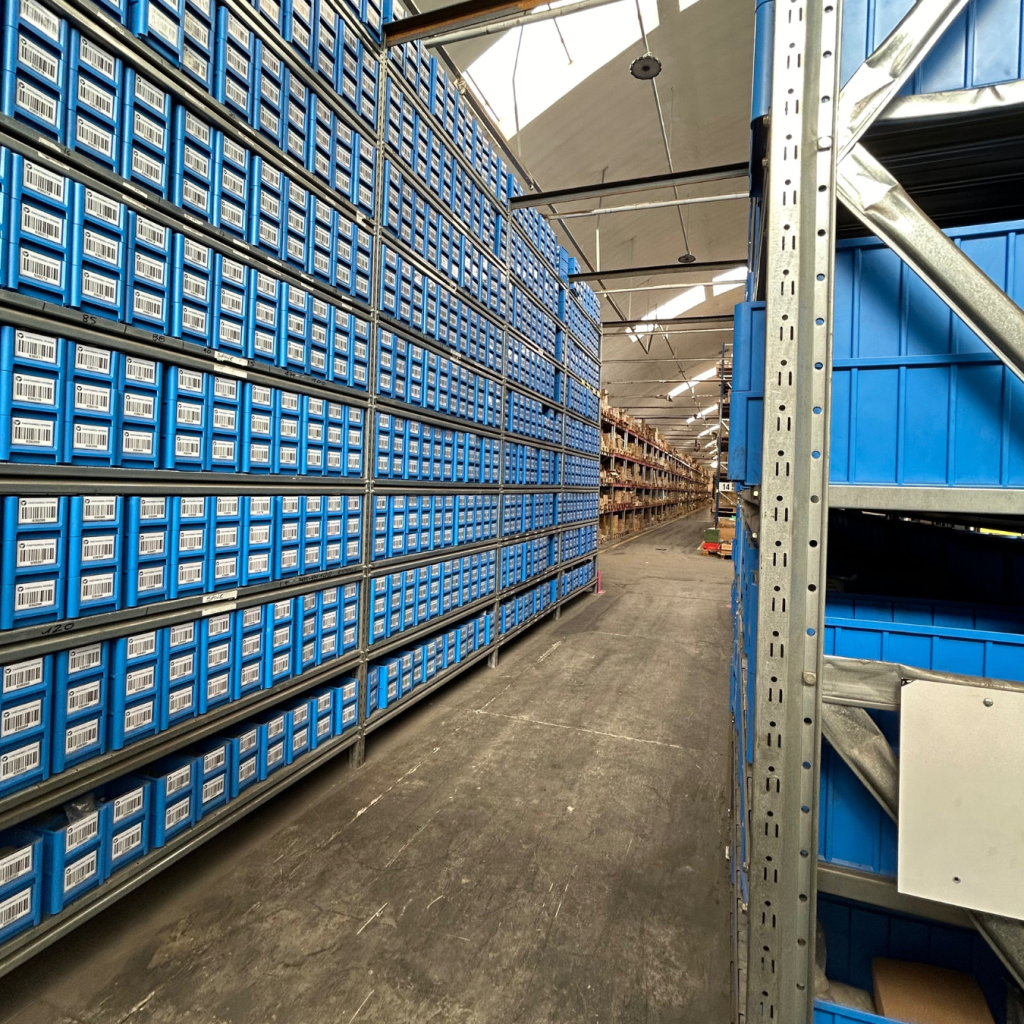
Definition and origin of the Kanban system
Japanese engineer Taiichi Ohno developed the Kanban system, drawing inspiration from the inventory practices used in American supermarkets. In these settings, customers select products from labeled shelves, and after making a purchase, information about the store's stock levels is recorded. This system allows for automatic replenishment orders to be generated for the warehouse. The effectiveness of this process is due to the shared labeling system between the warehouse and the point of sale.
Subsequently, the warehouse sends replenishment orders to suppliers or manufacturers, initiating a cycle that involves the entire supply chain. The ultimate goal is to ensure that products are available at the points of sale. To maintain control over inventory and prevent "empty shelf" situations, it is essential to establish well-defined reorder points.
The Kanban system for fasteners
The fundamental principle of this production line replenishment system is simple yet highly effective: it uses a rotation system with two containers to ensure screws are made available just in time directly at the storage station. Once the material in the first container is depleted, the second container is already in place, as Castagnoli has replenished the shelf before the first container runs out. This approach allows for:
- Respond promptly to changes in demand
- Ensure safe supply
- Reduce warehouse stocks
- Optimize the use of capital.
The materials flow is managed with exceptional simplicity using a system of two containers, each equipped with a Kanban label and supported by barcodes. All relevant data, including customer information, storage location, item details, product name, container type, batch number, and fill quantity, are recorded with the utmost precision.
The Kanban system
The Kanban system, an essential component of the Just-In-Time (JIT) methodology, is utilized to optimize procurement and stock replenishment phases. This approach aims to enhance the efficiency of production processes by ensuring the availability of raw materials at the right time. Its primary objective is to align production capacity with actual demand, thereby reducing overproduction and minimizing downtime between processing phases.
It is primarily applied in contexts characterized by a pull-based logic, where production starts only after receiving a final order from the customer.
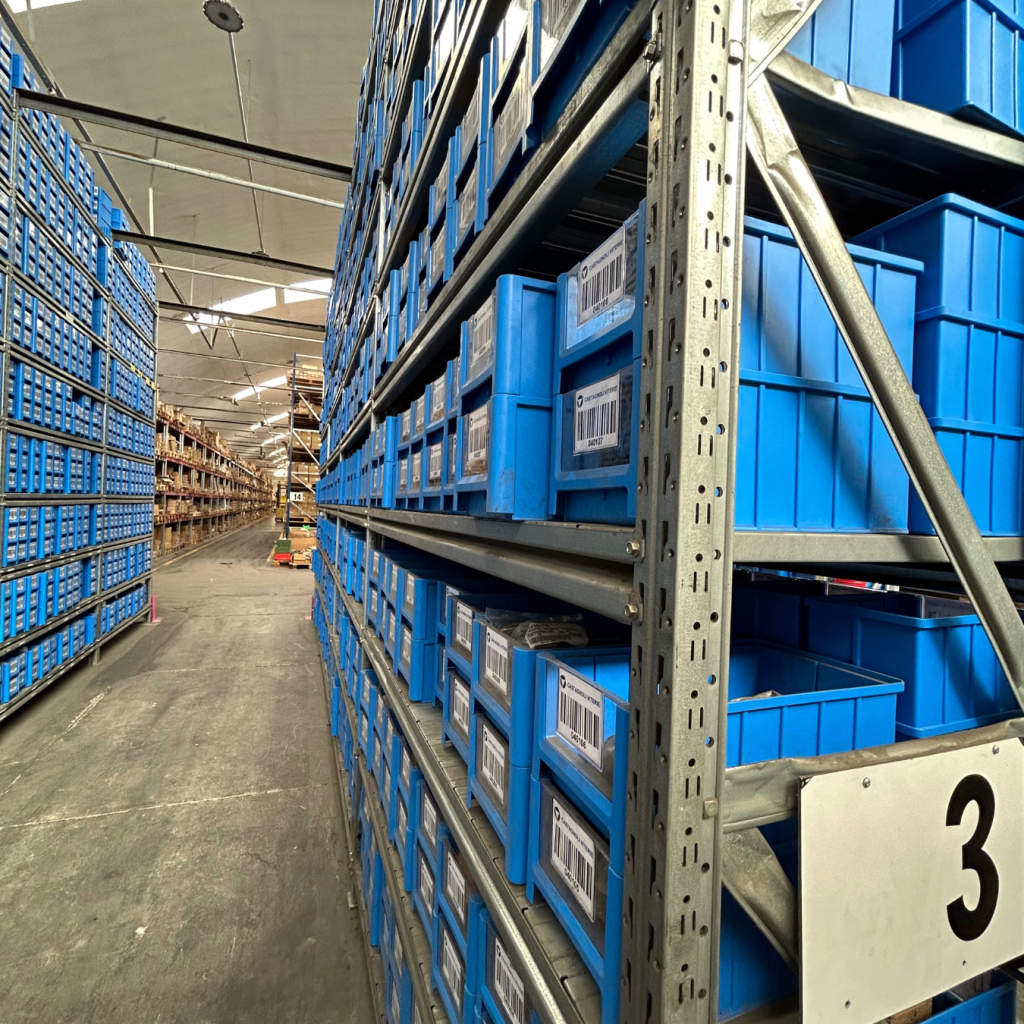
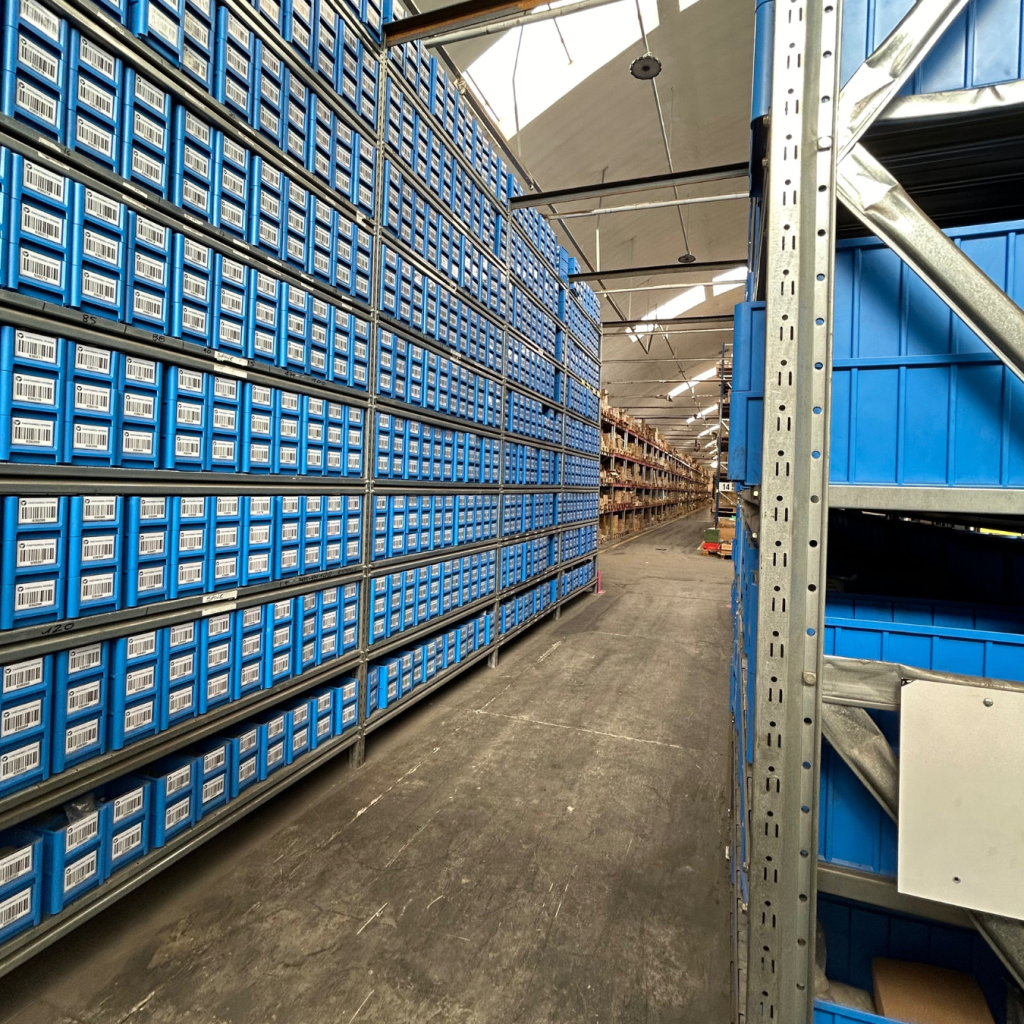
Definition and origin of the Kanban system
Japanese engineer Taiichi Ohno developed the Kanban system, drawing inspiration from the inventory practices used in American supermarkets. In these settings, customers select products from labeled shelves, and after making a purchase, information about the store's stock levels is recorded. This system allows for automatic replenishment orders to be generated for the warehouse. The effectiveness of this process is due to the shared labeling system between the warehouse and the point of sale.
Subsequently, the warehouse sends replenishment orders to suppliers or manufacturers, initiating a cycle that involves the entire supply chain. The ultimate goal is to ensure that products are available at the points of sale. To maintain control over inventory and prevent "empty shelf" situations, it is essential to establish well-defined reorder points.
The Kanban system for fasteners
The fundamental principle of this production line replenishment system is simple yet highly effective: it uses a rotation system with two containers to ensure screws are made available just in time directly at the storage station. Once the material in the first container is depleted, the second container is already in place, as Castagnoli has replenished the shelf before the first container runs out. This approach allows for:
- Respond promptly to changes in demand
- Ensure safe supply
- Reduce warehouse stocks
- Optimize the use of capital.
The materials flow is managed with exceptional simplicity using a system of two containers, each equipped with a Kanban label and supported by barcodes. All relevant data, including customer information, storage location, item details, product name, container type, batch number, and fill quantity, are recorded with the utmost precision.
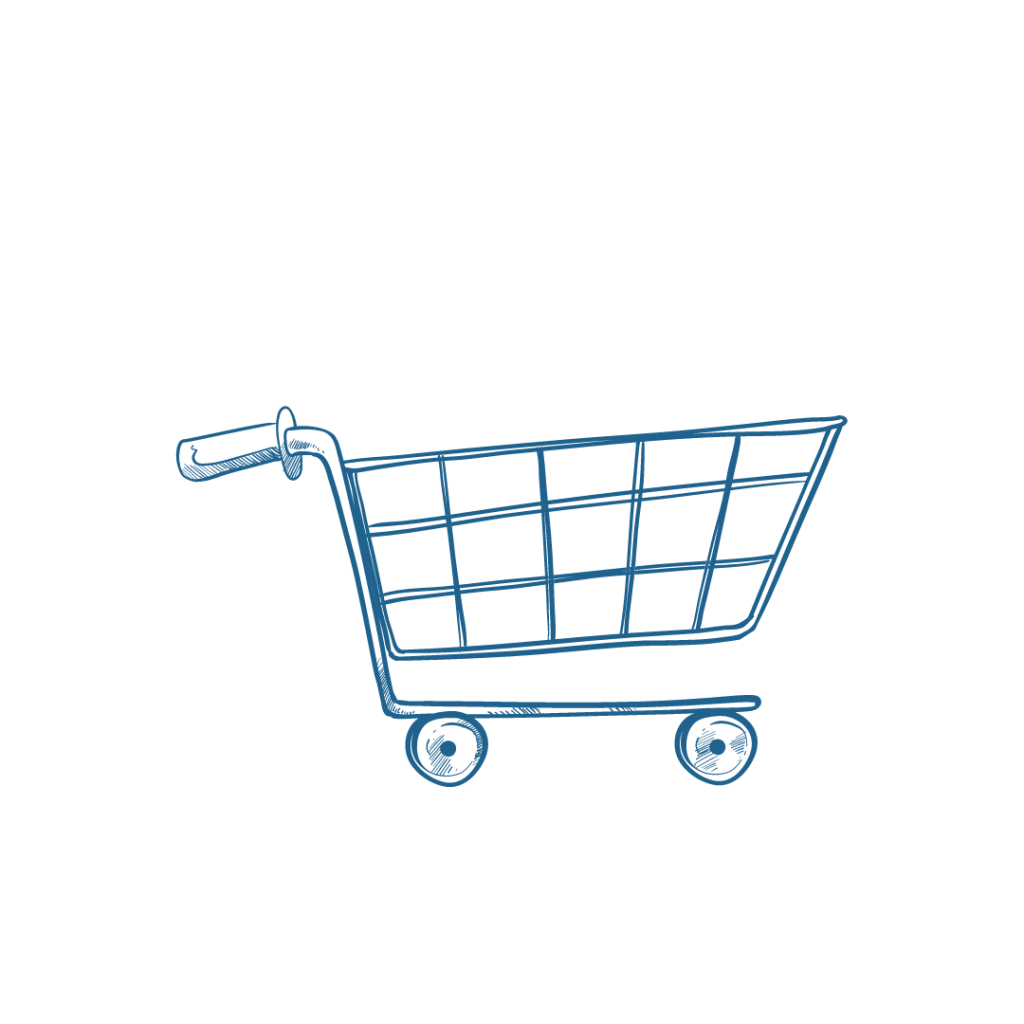